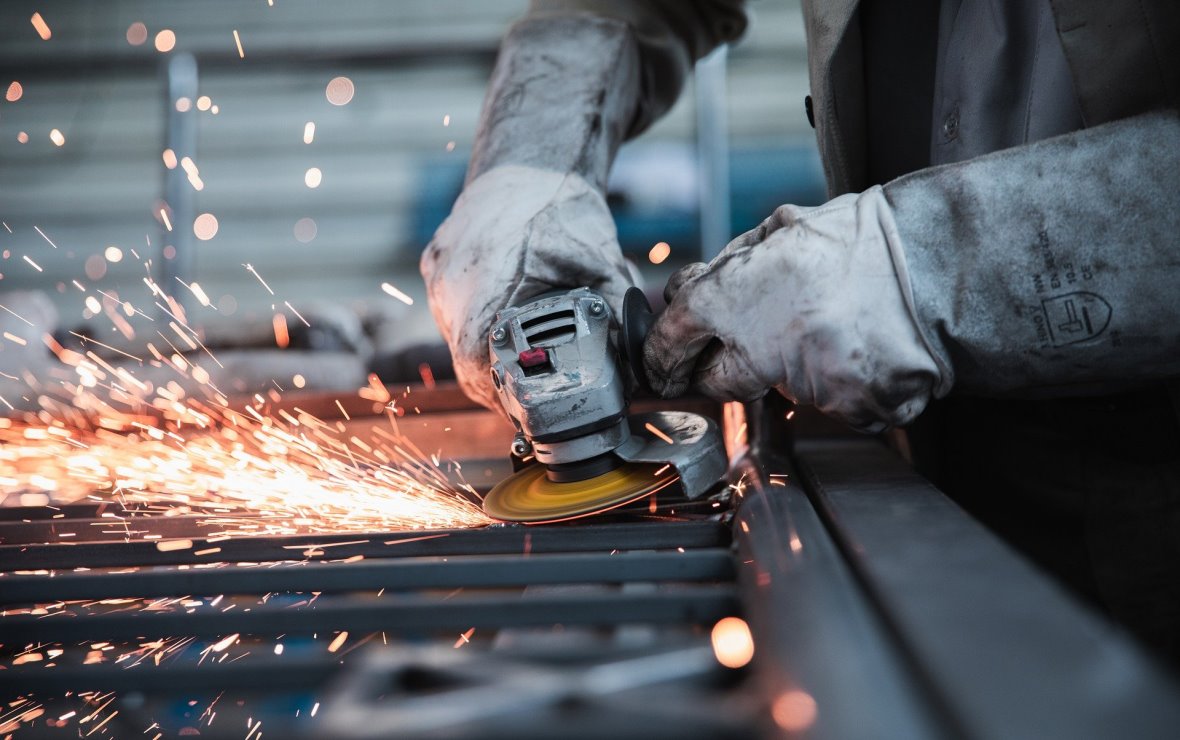
Национальный проект «Производительность труда», призванный к 2024 году создать условия для ежегодного прироста трудовой выработки в стране на 5%, был утвержден майским указом президента в 2018 году. В том же году Липецкая область вместе с еще 15 российскими регионами стала пилотной площадкой для реализации проекта — тогда на радикальные перемены решились лишь 10 предприятий. По итогам 1 квартала 2021-го таких предприятий — уже почти 60 (обрабатывающие производства, агропредприятия, строительные компании, предприятия сферы ЖКХ и автотранспорта), а область заняла четвертую строчку в рейтинге 69 субъектов РФ, участвующих в нацпроекте. Предприятия Липецкой области рассказали РБК Черноземье, с чем пришлось столкнуться в процессе внедрения стандартов бережливого производства и много ли нужно для получения заметных результатов.
«Признать наличие проблем»
В рамках реализации проекта предприятия региона получили доступ к целому спектру мер поддержки: льготным займам и кредитам на техперевооружение, грантам до 300 млн рублей от фонда «Сколково», налоговым преференциям, программе поддержки автоматизации и использования цифровых технологий, а также адресной поддержке по оптимизации производственных процессов и культуры производства на предприятиях. При этом почти все из опрошенных РБК Черноземье участников проекта были единодушны во мнении — самые большие резервы производительности не связаны с финансами. В областной администрации также отметили, что наибольшая эффективность от мероприятий по повышению производительности труда, измеряемая как соотношение затрат к полученному результату, получена за счет повышения организационной культуры предприятий.
Отчасти, считают эксперты, такой феномен можно объяснить эффектом «низкой базы». «В сложившейся производственной культуре можно выделить целый ряд организационных недостатков, — говорит директор Липецкого регионального центра компетенций в сфере производительности труда Александр Вартанян. — А можно просто сказать, что она находится в зачаточном состоянии. Очень слабо построена система аналитики проблем. Практически не анализируется график полезного времени работы оборудования. И что самое главное — не ведется систематический комплекс мероприятий по повышению эффективности труда сотрудников, включая работу с рацпредложениями по улучшению текущих процессов. У предприятий отсутствует среднесрочная стратегия развития — руководители «тонут» в текущих проблемах, не уделяя достаточного внимания средне- и долгосрочным целям, и зачастую не готовы признать наличие проблем».
Впрочем, отмечает эксперт, эта ситуация не является специфичной для липецкого региона. О тех же проблемах говорит опыт работы Центров компетенции в 54 субъектах РФ.
«Внедрение производственной культуры — небыстрый и сложный процесс, но именно он формирует базу дальнейшего развития, которую не всегда можно получить даже путем проведения полной модернизации производств, — подчеркнули в администрации Липецкой области. — Не секрет, что на многих японских производствах до сих пор работают станки 50-80 годов прошлого века, обеспечивая при этом высочайшее качество именно за счет производственной культуры организации и сотрудников».
Именно развитие производственной культуры и стало наиболее востребованным видом экспертной поддержки среди предприятий — участников проекта, констатирует Александр Вартанян. В него включены и оптимизация потоков, и обучение, и работа по целеполаганию, и управление изменениями. Используемая специалистами Центра компетенций методика базируется на работах российских ученых — основоположников НОТ, а также на зарубежном опыте Тайити Оно (Тойота), У. Деминга, У Шухарта, С. Синго и многих других.
«Все любят постоянство и никто — движение вперед»
Второй по важности фактор влияния на процессы оптимизации производства — отношение к нему персонала предприятий.
«В человеческом капитале заложен самый большой ресурс для любых изменений, — уверен управляющий компании «Электрома» Константин Мелешко. — Внедрение новых принципов производства у нас в компании встретило некую пассивность со стороны сотрудников, но это нормальное состояние, которое никогда не преодолеть. Процесс улучшений непрерывен, а все любят постоянство и никто — движение вперед. Впрочем, на кадровой стабильности это не сказалось — никто не уволился. За два с лишним года, что мы в проекте, производительность труда выросла в среднем на 15%, хотя и наши стартовые показатели были неплохи для отрасли. И это не считая того, что сложно оцифровать, но что серьезно экономит время и ресурсы — например, умение ставить и обсуждать проблемы. Подчеркну — все это только за счет организационных мер, без привлечения финансов. И самое главное — сформировалось проактивное «ядро» сотрудников, порядка 10% человек, которые откликнулись и активно участвуют в работе. Это — уже немало для масштабирования перемен».
«Многим сотрудникам в слове «оптимизация» слышалось «сокращение», но этот фактор тревожности ушел после первых же тренингов со специалистами Центра компетенций, — делится опытом руководитель проектного офиса «Производительность труда» Агрофирмы «Липецк» Александр Селезнев. — Люди увидели свою выгоду, и это свело на нет весь негатив. Сейчас из 300 сотрудников компании проактивными являются руководители начального звена — мастера, бригадиры. Линейный персонал пока не очень уверен в себе, страх предложить неудачную идею все еще силен, но, думаю, преодолим».
«Идеи, которые ничего не стоят, но многое дают»
В том, что копейка миллион сбережет, убедились почти все участники проекта по внедрению бережливого производства. Многие найденные в ходе проекта решения оказались настоящими лайфхаками с точки зрения соотношения внедренческих затрат и полученного эффекта.
«Специалисты Центра компетенций смогли «вытащить» из производственной рутины внутренние резервы и показать нам наши проблемы, ставшие нормой, — признает Александр Селезнев. — Например, мы тратили почти 200 тысяч рублей на упаковочные пакеты для скорлупы на инкубаторном производстве и задействовали на этом участке двух человек. Решением проблемы стало изготовление ручного пресса для скорлупы и покупка мусорного контейнера, а итогом — высвободившаяся трудовая единица, экономия на упаковке и минимизация экологического вреда. С завершением полугодового цикла работы со специалистами ФЦК мы продолжили работу в этом направлении. Например, на энергоучастке сотрудники предложили идею, внедрение которой стоило 10 тысяч рублей, а позволило экономить 500 тысяч рублей ежемесячно».
Одним из самых показательных кейсов по итогам работы в рамках нацпроекта стали результаты ООО «ГК «ЛипецкПрофиль». Компания присоединилась к проекту в начале июля 2020 года, а уже в декабре на поток-образце по оптимизации линии производства вентилируемого фасада производительность труда (выработки) выросла на 429% — с 7 до 30 кв. м на человека, время протекания процесса сократилось на 52%, объем запасов и незавершенного производства уменьшился на 35%, оборачиваемость складов выросла на 25%.
«Стоимость этих решений — примерно 25 тысяч рублей, потраченных на таблички, уголки и фанерные листы, — пояснил Александр Вартанян. — А экономический эффект оценивается миллионами рублей».
Предприятие ООО «СтальСоюз» в сотрудничестве с АНО «РЦК» Липецкой области также успешно реализовало комплекс мероприятий в рамках нацпроекта «Производительность труда» и сократило время протекания рабочего процесса на 34,4%, повысило выработку на 20%, а оборачиваемость склада — на 15%.
«Агрофирма ТРИО» и «Елецкий» за шесть месяцев проекта внедрили принципы бережливого производства в процессы сортировки и отгрузки чипсового картофеля. В рамках реализации проектов с применением методик и инструментов ФЦК за полгода удалось достичь значительных результатов. На предприятиях сократили время протекания процесса отгрузки автомашин на 34% и 24% соответственно, сократили запасы товарно-материальных ценностей на 32% и 45%, увеличили выработку на 1 человека на 63% и 30%, а также сократили возвраты некачественной продукции на 100% по обоим предприятиям.
«Мы все привыкли четко, стабильно выполнять текущие дела, но как оказалось, можно делать еще лучше. Ознакомившись с принципами бережливого производства, с тем, что делает ФЦК, мы увидели потенциал роста производительности. Именно правильно выстроенная система с методологией и инструментами поможет сделать наше производство более эффективным, — отметил Виктор Ретинский, управляющий директор ООО «Агрофирма ТРИО» и ООО «Елецкий». — На достигнутом останавливаться не намерены, уже составлен план реализации новых проектов на три года, будем тиражировать полученный опыт и дальше».
Немаловажно, что сотрудники компаний, участвующих в проекте, ощутили и материальные преимущества от внедренных решений. Как пояснили в администрации области, по мониторингу предприятий, находящихся на пути становления производственной системы, четко прослеживается рост выработки на одного сотрудника и снижение уровня брака, что при сдельно-премиальной системе оплаты труда, принятой на большинстве производств, приводит к росту уровня заработной платы. Впрочем, материальная стимуляция работает лишь до определенного уровня, напоминает Александр Вартанян. Впоследствии на первые роли выходит нематериальное поощрение — дипломы, ценные подарки, благодарности, карьерный рост, и этому тоже уже есть ряд примеров.
Резюмируя текущие итоги проекта, в администрации области подчеркнули, что экстенсивный путь развития, связанный с совершенствованием только материальной базы, сегодня уже малоэффективен. Лучший результат показывает именно комплексный подход, нацеленный на развитие как средств производства, так и человеческого потенциала.