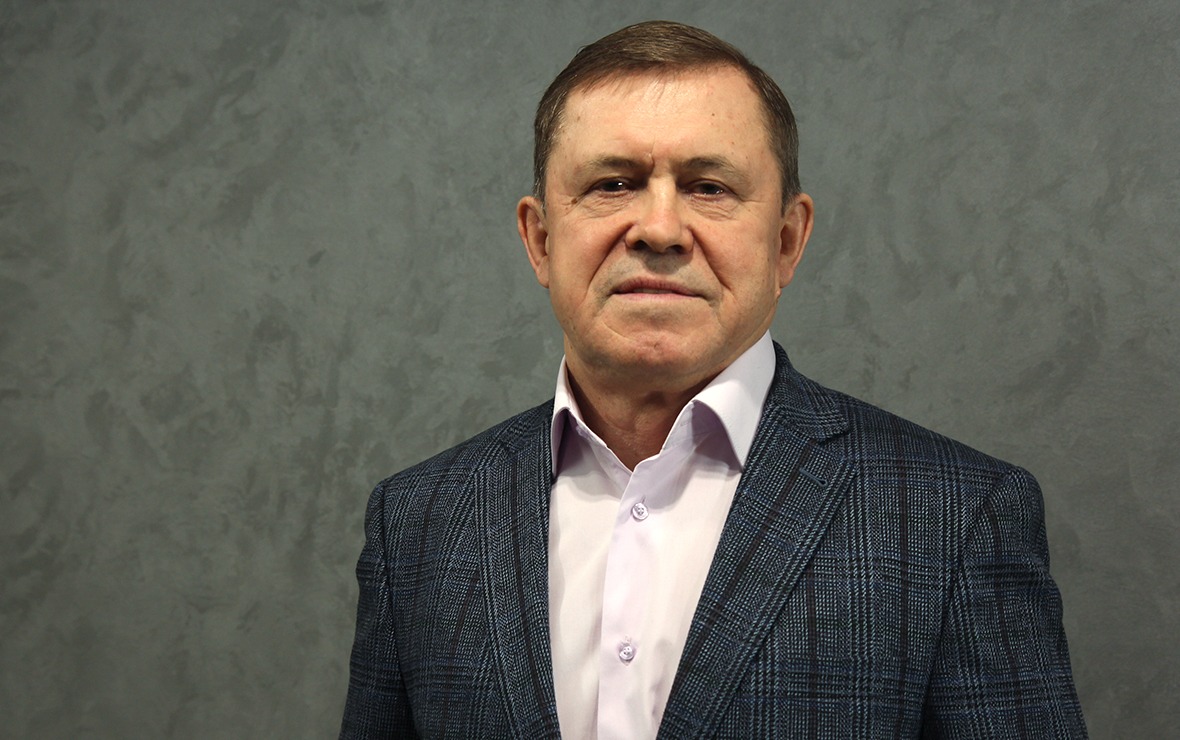
— Белэнергомаш производит «начинку» как для отечественных объектов тепловой и атомной энергетики, так зарубежных. Каково сейчас соотношение зарубежных и российских заказов в общем портфеле предприятия? Какие заказы хотели бы получить в будущем?
— Все верно, мы выпускаем оборудование для тепловой и атомной энергетики, но не только. В структуре предприятия есть еще пять современных производств: по изготовлению металлоконструкций, котельного оборудования, сильфонных компенсаторов, кузнечно-прессовое производство и собственные мощности по выпуску труб.
Завод имеет самый большой в стране опыт производства трубопроводов для АЭС — более 45 лет. Модернизация трубопроводного производства в 2015 году с вводом 45 тысяч квадратных метров производственных площадей позволила усовершенствовать технологические процессы производства, увеличить производительность труда и сократить время изготовления продукции. Если говорить о структуре заказов, на экспорт поставляем блочные трубопроводы для атомных станций, которые строит за рубежом госкорпорация «Росатом».
Сегодня мы участвуем в таких проектах, как строительство АЭС «Куданкулам» в Индии, «Руппур» в Бангладеш, первого и второго блоков АЭС «Аккую» в Турции. В следующем году начнем поставки блочных трубопроводов для двух новых блоков атомных станций «Тяньвань» и «Сюйдапу» в Китае, а также для АЭС «Пакш» в Венгрии. В том числе участвуем в первом пилотном проекте России — это ВВЭР-ТОИ, Курская АЭС-2.
Кроме того, производим трубопроводы для крупнейшей тепловой электростанции Красноярского края — филиала «Березовская ГРЭС». Мы и в дальнейшем готовы наращивать объемы производства исходя из потребностей рынка.
Несмотря на трудности, внесенные пандемией, 2021 год мы заканчиваем достаточно успешно. Во втором полугодии набрали уверенные темпы, и по итогам четвертого квартала намерены выйти на все плановые показатели. На предприятии сформировался крепкий коллектив высококвалифицированных специалистов. Мы стараемся обеспечить людей не только стабильной работой, но и создаем все необходимые условия для труда и профессионального развития.
— Вы сейчас активно развиваете производственную систему. Насколько нам известно, уже реализовано семь проектов по повышению эффективности в производстве металлоконструкций и складе материалов, внедрены новые инструменты ПС. Поделитесь результатами, как это отразилось на качестве производства?
— Мы называем эту систему бережливым производством, или программой постоянного совершенствования. На предприятии с 2014 года действует собственное подразделение — управление по развитию производственной системы Энергомаш. За это время проделана большая работа. На данный момент завершен проект по повышению производительности труда в производстве соединительных элементов трубопроводов. Продолжаем работу по внедрению «бережливых» технологий в производстве металлоконструкций. Уже достигнуты положительные результаты по повышению производительности труда на 15%. Также мы осуществили масштабную модернизацию котельного производства, в которую вложили около 1 млрд рублей. В результате выпуск продукции увеличился практически вдвое.
С мая этого года я одновременно являюсь управляющим директором завода ОМК в Челябинске (завод «ОМК Трубодеталь»). Это крупнейший в стране производитель соединительных деталей трубопроводов для нефтегазовой отрасли. Здесь уже несколько лет с успехом внедряются принципы бережливого производства, ведется обучение персонала. По итогам аудита японской компании Toyota Engineering Corporation в 2019 году завод отмечен бронзовой медалью за развитие производственной системы. Белгородские специалисты выезжают на предприятие для обмена профессиональным опытом и лучшими практиками, организованы встречные стажировки специалистов. Отмечу, что в течение года мы обучили около 500 человек новым методам и подходам бережливого производства.
Еще один важный момент: в текущем году, к сожалению, мы столкнулись с серьезным ростом цен на металлопродукцию, сырья для нашего производства. Безусловно, это негативно сказывается на себестоимости и прибыли предприятия. Поэтому применение современных технологий бережливого производства в текущих условиях позволяет нам не только исключать потери, но и сохранять рентабельность и доходность предприятия.
— В этом году вы закрыли цех горячего цинкования. В связи с чем принято данное решение? Можете оценить экологический эффект?
— Верно, в начале года мы закрыли линию горячего цинкования, которая действовала в производстве металлоконструкций с 2001 года. На тот момент в общем портфеле заказов предприятия около половины всех продаж приходилось на оцинкованные металлоконструкции. В настоящее время большого спроса на такие услуги у нас нет. Цинкование в заказах применялось очень редко. Нашим потребителям, которые занимаются строительством социальных объектов разного назначения (аэропорты, стадионы), как правило, требуются металлоконструкции с современным покрытием — большой слой защиты с хорошей подготовкой. Для предприятий нефтегазового комплекса — огнезащитные покрытия. Поэтому высвободили площади именно для этих целей.
К тому же за 20 лет эксплуатации цеха оборудование сильно изношено и нуждалось в глубокой модернизации. Взвесив все «за» и «против», мы решили полностью вывести его из эксплуатации. Стоит отметить, что с точки зрения экономической целесообразности этот участок не приносил большой прибыли.
Ходило много разных кривотолков и слухов: «Почему ликвидируют?», «Что будет с рабочим персоналом?». Всем сотрудникам было предложено продолжить работу на предприятии. Они перешли на другие аналогичные производства. Конечно, были и те, кто решил уволиться по собственному желанию, поскольку им был нужен стаж по вредному труду. Важно, что с ликвидацией участка мы смогли сократить выбросы загрязняющих веществ в атмосферу Белгорода на 2,8 тонн в год и уменьшить количество отходов 2-4 класса на 350 тонн в год. И в этом смысле наш завод идет в ногу со временем, руководствуясь при принятии инвестиционных решений еще и заботой об окружающей среде в рамках общей повестки устойчивого развития.
— Давайте поговорим о социальной политике «Белэнергомаш-БЗЭМ». В этом году в Белгороде впервые прошел конкурс социальных и благотворительных проектов «ОМК-Партнерство». Поделитесь, в чем его основная идея? Какие инициативы представили белгородцы, и как они будут воплощаться в жизнь?
— С начала 2020 года мы входим в Объединенную металлургическую компанию (ОМК). Компания многие годы реализует системные социальные программы, которые помогают развивать регионы, где работают ее предприятия. Это и инфраструктурные проекты для создания комфортной среды, и культурно-образовательные программы, и социальные и благотворительные проекты.
В этом году мы впервые провели в Белгороде грантовый конкурс социальных и благотворительных проектов «ОМК-Партнерство». Он направлен на поддержку проектов некоммерческих и муниципальных организаций, социальных проектов наших сотрудников. От Белгородской области на конкурс заявили 29 проектов, 13 из них получили финансирование ОМК в размере до 250 тыс. рублей. Речь про проекты в сфере физической культуры и массового спорта, дополнительного образования и воспитания детей, благоустройства территорий и другое.
Также мы помогаем белгородским медучреждениям, особенно детским больницам и поликлиникам. Активно принимаем участие в деятельности межрегиональной общественной организации «Святое Белогорье против детского рака», которая помогает детям с онкологическими и тяжелыми неизлечимыми заболеваниями.
Сейчас наше предприятие выступило спонсором команды КВН Белгородской области. Мы регулярно поддерживаем различные региональные спортивные и социальные мероприятия, а также проекты, направленные на улучшение комфортной среды. Помимо этого, особое внимание уделяем развитию физической культуры и спорта среди сотрудников. На территории предприятия действует собственный спортивный комплекс и фитнес-зал, который постоянно посещают порядка 400 человек.
— Раз мы заговорили о сотрудниках вашего предприятия, какие еще социальные инициативы реализованы для персонала?
— Мы стараемся создавать комфортные условия труда для сотрудников — начиная от закупки качественного оборудования до организации удобного рабочего пространства. Сейчас практически завершили ремонт бытовых помещений — раздевалок и душевых комнат. Людям нужно обеспечить достойные условия, где они смогут отдохнуть после смены, принять душ, переодеться.
Ввели для сотрудников дотацию на питание более 80 рублей в день за счет предприятия. Ко Дню машиностроителя открыли новую современную столовую на площадке №1. Отдельное помещение для приема пищи обустроили на производственной площадке металлоконструкций. Правильно организованное горячее питание на предприятии — важнейшая составляющая рабочего процесса. Люди это ценят.
Кроме того, на территории предприятия открыли медико-санитарную часть. Если раньше мы привлекали профильных врачей для плановых медицинских обследований, то теперь все сотрудники смогут получить необходимую медицинскую помощь на месте.
— В этом году «Белэнергомаш — БЗЭМ» инвестировал в модернизацию производства около 1 млрд рублей. На что конкретно были направлены средства, и каковы параметры инвестпрограммы на следующий год?
— Для успешного функционирования любого промышленного предприятия машиностроительного профиля процесс обновления производственных фондов должен быть непрерывным. Сегодня меняется оборудование, совершенствуются технологии, повышаются требования к производству. В том числе усложняется и процесс исполнения заказов по срокам. В борьбе за заказчика, как правило, побеждает то предприятие, которое в перспективе может обеспечить своевременную поставку качественного оборудования.
Поэтому сегодня мы ведем серьезную работу по модернизации основных производственных мощностей. В первую очередь стараемся совершенствовать те площадки, где видим высокую динамику по портфелю заказов. Мы уже завершили процесс обновления трубопроводного и котельного производств, создали новый участок опорно-подвесных систем, частично модернизировали литейное производство.
На данный момент основная часть инвестиций направлена на завершение последнего этапа модернизации металлургического комплекса. Планируем установить современный ковочный комплекс — пресс и манипулятор. Мы изготавливаем трубы методом электрошлаковой выплавки и методом ковки. В целом все комплексные решения, которые принимаем, ориентированы на обновление оборудования под конкретные технологии. Только совершенство продуманных решений обеспечивает эффективность инвестиций и их окупаемость.